Processing
Furthermore, the company is committed to providing safe, high-quality products produced under socially responsible conditions. In 2016, it refined its social standards, pushed forward with their implementation, and improved its recipes.
It is important to Migros that its products are produced under good working conditions. It therefore stipulates that its suppliers adhere to certain social standards. For textile own brands, all its suppliers must follow the Eco guidelines. Migros also makes sure that the products made by M-Industry contribute towards a balanced diet.
In the area of social standards, Migros' actions are based on the UN Guiding Principles on Business and Human Rights, which provide companies with a framework for respect of human rights and working conditions in the supply chains. As a member of the UN Global Compact and a founding member of the Business Social Compliance Initiative (BSCI), Migros fulfils its responsibility to comply with social standards.
On the basis of the BSCI, Migros demands that all suppliers and producers meet the minimum social requirements of the BSCI Code of Conduct or equivalent requirements. This forms part of the basic requirements and is gradually being implemented in all Migros Group companies. Migros integrates its business partners into the BSCI process on the basis of a risk assessment that takes into account the type of supply chain, the country of production, the industry and the sales volume.
A key element of the UN Guiding Principles is human rights due diligence. In Cooperative Retailing, this is incorporated in the business processes as part of the sustainability strategy. In 2016, Migros analysed the value chains of various raw materials according to environmental, economical and social aspects. The identified human rights touchpoints are taken into account in the product range decision; any negative aspects are offset by various standards and labels. In addition to the main social standard BSCI, this also includes labels such as UTZ, Max Havelaar and FSC.
BSCI audits: results within the sector average
In 2016, the Migros Group companies conducted a total of 713 BSCI audits (2015: 425), the majority of which were in India and China. 86 companies (12%) achieved good results in the audits. Minor non-conformities were found at 526 companies (74%), and 101 companies (14%) need to correct more serious problems. These figures are within the sector average. In the reporting year, a new rating scale with five levels (A to E) was applied to the companies.
BSCI audits
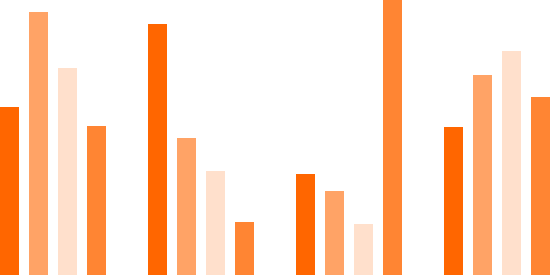
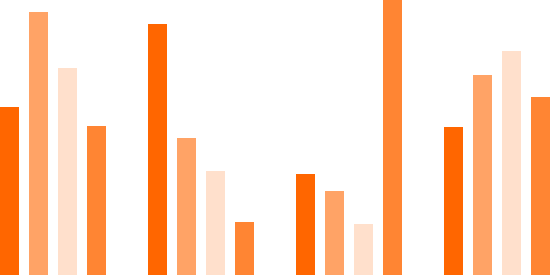
In 2016, numerous factories were assessed by means of internal factory inspections, rather than BSCI audits. In India, for example, 17 factory inspections were carried out by Migros specialists. Alongside BSCI audits and factory inspections, the retailers also use other recognised social standards, such as SA8000, Sedex and SIZA, to ensure correct working conditions in the supply chains.
Migros carried out a total of 77 factory inspections worldwide. It also made an active contribution to strengthening the system integrity of BSCI as part of various BSCI committees and working groups. It participated in the development of guidelines to exclude passive members from the BSCI community. Migros also represented the Swiss network of BSCI members.
In the reporting year, members of the Consumer Goods Forum (CGF), including Migros, integrated the Global Social Compliance Programme (GSCP) into the work of the CGF as a strategic focus, and set priorities to abolish forced labour in the supply chains. GSCP guidelines provide orientation during implementation.
Through the implementation of the BSCI in high-risk countries, Migros also makes an active commitment to the issue of forced and child labour. Non-conformities in the two areas are rare these days; in the reporting year, the audits found just seven cases (forced labour) and two cases (child labour). Seven out of nine factories in which non-conformities were identified in 2015 and with which Migros still works, met the requirements in the reporting year. Most of the non-conformities at Migros' supplier companies are found in the areas of maximum working hours and management systems.
BSCI audits: breakdown by type of non-conformity
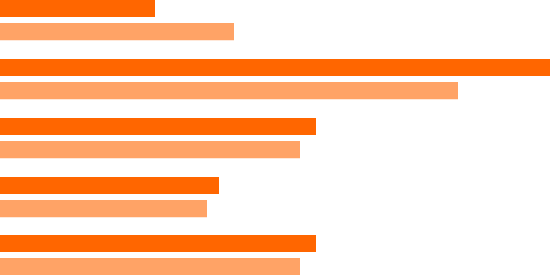
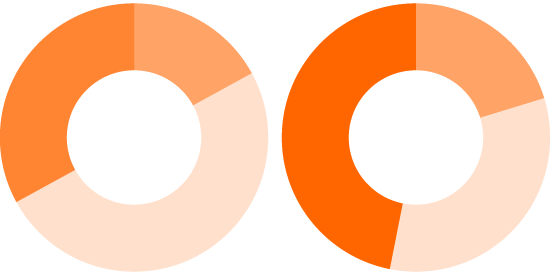
Migros maintains close dialogue with its stakeholders, which include numerous NGOs and universities. In 2016, it was made aware of issues in the production of pans in China. A specialist from the Migros procurement office in Hong Kong and an independent BSCI representative visited the factories and identified problems with the documentation, as well as unclear processes, such as working hours incorrectly recorded. Appropriate measures were defined with the factory management, and their implementation will be assessed during the next audit.
Capacity building: training and empowering suppliers
As part of the development approach, Cooperative Retailing provides training, factory visits and courses to help its suppliers implement social standards. 85 workshops were held in 2016. In addition to personal interaction, Migros will assess technical solutions this year that will enable employees to obtain information directly about relevant issues, such as occupational health and safety and working hours. This will give them the opportunity to acquire knowledge individually.
Transparent supply chain
In order to monitor working conditions in the production plants, Migros needs to know where the products are produced. As the supply chain often involves several intermediaries that do not always wish to disclose the identity of their manufacturers, full transparency is difficult to achieve. Furthermore, the supplier portfolio is constantly changing: new suppliers are added and existing ones delisted. In 2016, the Migros Group managed to reduce the proportion of non-transparent supply chains to 22.5% (2015: 34.0%). Overall, Migros worked with 8'702 suppliers. 3'210 of these suppliers (36.9%) have potentially risky supply chains.
In potentially risky supply chains, the production plants are located primarily in a high-risk country, such as India, China or Eastern Europe, with production processes that involve a great deal of manual labour. The definition of a high-risk country is based on the World Wide Governance indicators of the World Bank, which consider aspects such as corruption, rule of law and the implementation of legislation.
The Eco label, developed by Migros in 1996, stands for seamless documentation and traceability across all stages of the textile production process and ensures that no health or environment-critical substances are used.
At the end of 2016, 74.8% of all clothing produced in Cooperative Retailing carried the Eco label. As part of its sustainability promise, Migros has set itself the target of producing all own-brand textiles in an environmentally and socially sustainable and traceable way in accordance with the Eco label guidelines by the end of 2017.
The current situation does not reach the planned milestones, which is why this promise is not on track. As textiles are ordered with a lengthy lead time, it is already clear that the ambitious target cannot be met within the remaining timeframe. Although Migros is one of the sector's pioneers and already imposes stricter requirements on its suppliers than the sector average, it will continue to push ahead with its ambitious target. It has thus decided that, from 2018, it will recognise the international textile standards GOTS, bluesign, Made in Green by OEKO-TEX and IVN Best as equivalent to its own guidelines. Migros is convinced that this approach will lead to a faster implementation.
Compliance with Eco requirements is checked by independent third parties on behalf of Migros. All participants in the textile value-added chain are known. The standard aims to ensure that all stages of production, from yarn to finishing with details of the chemical products and production processes used, are documented, assessed and checked for compliance with Migros' requirements. By showing its suppliers how to handle harmful substances and chemicals, for example, and providing staff training, Migros helps to improve the relationships with suppliers and ensure traceability.
Migros improves its products continuously. Together with the suppliers, it launches improved products and thereby makes a contribution to a balanced diet. Thanks to its own industry, it is able to have a direct influence on the recipes.
Migros is aiming to offer more than 150 products with less sugar, salt and fat, but more fibre, by the end of 2018. Since 2013, it has improved 210 product recipes, in particular ready meals, dairy products, soup and muesli. This objective has been achieved and thus the promise was met ahead of schedule at the end of 2016.
Food safety measures are taken to ensure that food is suitable for consumption and will not impair the consumer's health in any way.
To ensure perfectly safe food, the Migros Group companies apply various standards during quality assurance, such as those certified by The Global Food Safety Initiative (GFSI). Most domestic and foreign third-party suppliers of processed foods, including the M-Industry companies, are certified according to a standard recognised by the GFSI.
For the remaining suppliers, Migros carries out risk-based inspections. The standards recognised by the GFSI and the inspection requirements of Migros cover areas such as production hygiene and product safety guidelines to ensure food safety. In 2016, the implementation rate was 94.7% in M-Industry, 92.4% in Commerce and 94.8% in Cooperative Retailing.
In addition, Migros and its suppliers have their products continuously monitored during introduction and sale. On behalf of Migros, Swiss Quality Testing Services (SQTS) subjects the products to risk-based tests as part of self-regulation. Using a modern analysis method, SQTS checks the quality and safety of the products and whether they conform to the applicable laws.
In 2016, Cooperative Retailing performed around 18'00 product tests in total; 29 products had to be recalled due to non-conformities. These included Gorgonzola, for which the listeria limit was exceeded, and marzipan, rum and sultanas with chocolate, as the milk component was not declared for this product.
Research projects to increase food safety
Alongside research projects in the environmental field, Migros also supports projects that increase food safety. In the reporting year, a project to research the causes of tropane alkaloids in cereal production and find counter-measures was conducted at the Research Institute of Organic Agriculture (FiBL).
Another project focused on researching different pathogens. The aim is to broaden the basis of analysis and range of measures in the quality assurance of food originating from animals and plants that is intended for raw consumption. Migros expects the first findings this year.